Troubleshooting Air Suspension Problems in Heavy-duty Trucks: Tips and Techniques
Air suspension got you down? Fix it yourself with these troubleshooting tips for heavy-duty trucks! Learn to identify leaks, check valves & sensors, monitor pressure & more. Get your truck back on the road smoothly!
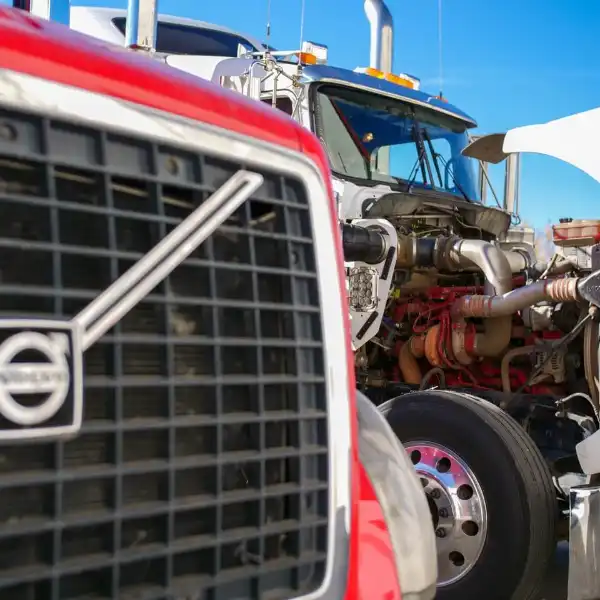
Heavy-duty trucks equipped with air suspension rely on a complex system of valves, lines, bags, compressors, and controls. When issues arise, pinpointing the root causes can be challenging. Here are effective troubleshooting tips for diagnosing air suspension problems:
Listen for Audible Clues
Pay attention to air leaks hissing from lines, valves, or bags which signal damage, allowing air loss. Also listen for the air compressor cycling frequently to maintain pressure, indicating a leak is present. Localize noise sources under the chassis.
Inspect Air Lines and Fittings
Air lines degrade and crack over time, causing leaks and pressure loss. Visually inspect all lines for damage. Check line connections for leaks using a soapy water spray to bubble test fitting tightness. Damaged sections or fittings must be replaced.
Check Air Bag Condition
Flat or leaking airbags allow the suspension to bottom out and sag. When deflated, inspect the bags closely for signs of cracking, ballooning when inflated, and chafed sections. Leaking or damaged bags must be replaced to avoid collapse.
Confirm Compressor Operation
A faulty compressor cannot generate sufficient air to maintain suspension pressure. Ensure the compressor engages when system pressure drops below the threshold and disengages once reaching the cutoff. Check output levels and electrically test the pressure switch if issues are found.
Inspect Valves
The various valves distribute and exhaust air for each airbag circuit. Clogged or damaged valves, such as ride height valves, dump valves, and quick-release valves, can make isolating leaks difficult. Inspect valve condition and test operation.
Check For Moisture Contamination
Excess moisture accumulation in the air tanks and valves from humidity causes corrosion and freezing in cold temperatures. Drain air tanks regularly and have the system periodically purged by a shop to avoid contamination issues.
Scan For Fault Codes
Modern air suspension systems have ECUs that store fault codes when issues are detected. Retrieving codes with a diagnostic scanner provides clues to defective component setting codes. Research codes to understand causes.
Assess Ride Height Sensors
Sensors monitor ride height and send input to the ECU to dynamically adjust air pressures. Damaged or dirty sensors can provide false data. Inspect the sensor condition and electrical connections. Compare sensor height readings.
Check For Sticking Control Valves
Solenoid valves distribute air to each bag. Sticking valves fail to open or close on command, making system adjustments erratic. Check valve electrical connections and test for sticking. Replace faulty ones.
Monitor Air Pressure Cycling
Viewing air pressure gauge fluctuation helps assess system operation. Pressures holding steady indicate leaks have been fixed. Erratic pressure variation points to air loss from a leak or faulty compressor operation.
Confirm No Loose Connections
Vibration causes electrical connections to loosen over time, interrupting the control unit and valve function. Check wiring harness connectors for a tight fit. Clean any corroded pins or terminals that need better contact.
Analyze Air Dryer Function
Contaminated air causes extensive system damage. The air dryer filters moisture from the air supply to keep lines clean and dry. Inspect desiccant beads and filters for saturation, which indicates a defective dryer.
Review Operational History
Determine what changes to the suspension preceded issues like ride height modifications or component replacements. Recent alterations help trace problems back to their origin for an accurate diagnosis.
Road Test the Truck
Test drive with gauges displayed to feel how the system reacts and view pressures live. Bottom-out suspensions over bumps to assess rebound. Have a second person inspect components which may be leaking only under movement and load.
Compare To Baseline
Compare current air pressures and ride heights to factory specs for each position, like kneeling, dumping, and raising. Any major deviations indicate improperly calibrated controllers or faulty levelling valves.
Check Air Delivery Time
Monitor how long the compressor takes to fill the air tanks from empty to cutoff pressure. Excessively long fill times indicate insufficient compressor output due to wear, low voltage, or underlying issues that need repair.
Inspect Linkages
Mechanical attachments between suspension components wear over time. Check for loose, bent, or broken sway bar links, control arms, and tie rods that hinder suspension articulation and levelling.
Assess Maintenance History
Review maintenance records for any neglected suspension service items. Lack of lubrication, old airlines, and unchanged desiccant point to overlooked maintenance, allowing deterioration.
Consider Contamination Damage
Contaminants like failed compressor oil seals damage air system components internally. Once contaminants are flushed, abrasive wear leaves valves and lines pitted and cracked.
Note Any Unusual Noises
Listen for odd sounds during compressor cycling and air exhaust indicating problems like worn bearing squeal or air blowing by clogged valves. Locate the sources of unusual noises.
Test in Various Conditions
Heat and altitude impact air delivery. Test in different seasons and locations to determine if ambient conditions exacerbate air loss. Thermal expansion can reveal small leaks.
Inspect Fasteners
Suspension components and lines work loose from road vibration over thousands of miles. Check for any loose or sheared bolts that allow air loss and instability.
Clear Diagnostic Codes
Erasing standing codes after repairs determines if issues have been reset. Any codes signal that signals the problem was not fully fixed. New codes point to additional faults.
Identify Aftermarket Modifications
Ask if any airlines or valves were rerouted or added for accessories. Improper modifications often cause air delivery problems mistaken as system failures.
Seek Professional Assistance
If in doubt, reach out to professional heavy-duty suspension mechanics. Their expertise will give you the peace of mind of knowing that your truck’s suspension is in capable hands.
Final words
Troubleshooting air suspension systems requires methodically isolating issues through inspections, tests, live readings, and diagnostic codes. Tracing problems back to single components is key for cost-effective repairs. Connecting symptoms to root causes prevents wasting time and money replacing the wrong parts. Proper repairs restore the smooth and stable ride quality essential for heavy truck operation.